PRV Repair
Pressure Relief Valves are designed to automatically protect your equipment against excessive over-pressure. Every care is taken in the service and setting of these valves to ensure complete dependability in performance. Our constant objective is to provide superior service that will assure ultimate protection/functionality at the lowest cost, both initially and throughout your valves service life.
Currently Rocky Mountain Valve Service and Repairs all makes and models of Pressure Relief Devices. Please contact your closest RMV Branch for more information, availability and turn around times.
service includes:
Initial Inspection |
Replacement of parts that require it. |
Initial Inspection
The initial inspection process tells us a lot about your valve. First and foremost it will tell us if there are any external leaks due to physical damage or corrosion. The condition of the inlet and outlet can help us determine if a improper installation has occurred causing physical damage to the inlet or outlet. The initial inspection also tells us if the proper valve was selected based on the service requirements supplied by the end user.
Pretest & Record
Pretesting is an integral part in determining if your valve is set on the proper service interval. How your valve behaves during a pretest can be affected by numerous things. Excessive fouling, Corrosion, fluid service, trim materials and length of time in service, these are just some of the things that can affect how your valve will operate inline. Pretesting determines how your valve is operating at the time of testing. Will your valve operate according to code or will it not. Your typical Section VIII valve should relieve within 3 percent of its set point for anything set over 71psi(490kPa). Anything outside of this allowable variation by code means that your valve has been affected by the service it is in and the service interval should be adjusted within the requirements set by ABSA's document AB-506(Inspection & Service Requirements for In-Service Pressure Equipment). For help in determining your service interval based on the information provided by RMV's test record, please contact your local RMV representative.
Dis-assembly
Only trained technicians can disassemble a PRD. Improper dis-assembly can cause internal damage to critical components of the valve causing additional repairs to be performed to bring your valve back to manufacturers specifications.
Component Critical Inspection
Each part will receive a visual examination for signs of wear and corrosion. Parts that show signs of excessive corrosion or wear will be replaced with genuine O.E.M supplied parts. All parts will be thoroughly cleaned with an appropriate method as to not damage the components. Particular attention will be paid to guiding surfaces such as stems, stem retainers, and guides. These surfaces should be free of corrosion or signs of pitting. Stems will be examined to determine if they are straight. The nozzle (body on screwed valves) will be examined to ensure there is no foreign matter that could restrict the valve's flow. All threads will be examined to make sure there is no damage that will interfere with assembly or operation of the valve. Flange facings will be examined for signs of damage that would inhibit proper sealing. Gaskets and soft goods, such as O ring seals will always be replaced if available.
Reconditioning/Replacement Of Parts
After each part has been inspected any deficiencies found will be recorded on the inspection report and it will be determined if the part can be repaired or requires replacement. To ensure proper valve performance, the nozzle (seat) and disc will be reconditioned within the original manufactures specifications. All gaskets and soft goods such as o-rings will be replaced with O.E.M or equivalent materials to ensure proper operation of the valve.
Machining
Machining is an integral step in maintaining O.E.M operational specifications. Machining occurs when critical and non-critical parts require major reconditioning due to excessive corrosion or excessive damage due to operational system failure. Machining parts can not only ensure the proper operation of your equipment but can save money and time. Unfortunately machining can only be done so many times before critical components do not fall under the original O.E.M specifications and at this time they will require replacement.
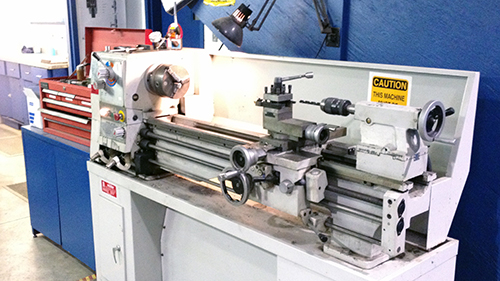
Assembly
Only trained technicians can reassemble a PRD. Improper reassembly can cause internal damage to critical components of the valve causing additional repairs to be performed to bring your valve back to manufacturers specifications.
Testing & Re-certification
Testing and Re-certification can only be done by a trained technician. All testing will be done in accordance with all applicable code and manufacturer requirements. All test information is recorded on the inspection report for future reference. Once set, each valve will be sealed to prevent tampering with the set point and blow down adjustment of the valve.

Final Inspection
Once your valve is complete, RMV will complete all documentation, paint and tag your valve in accordance with applicable codes and your specifications. RMV will mount your valve on a pallet or secure it in a container to ensure that it is shipped in a upright and secure position to prevent any unnecessary damage due to improper handling.
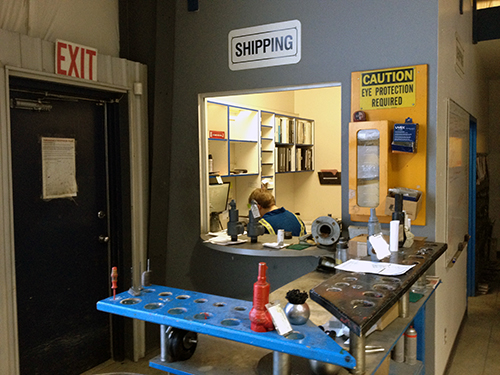